
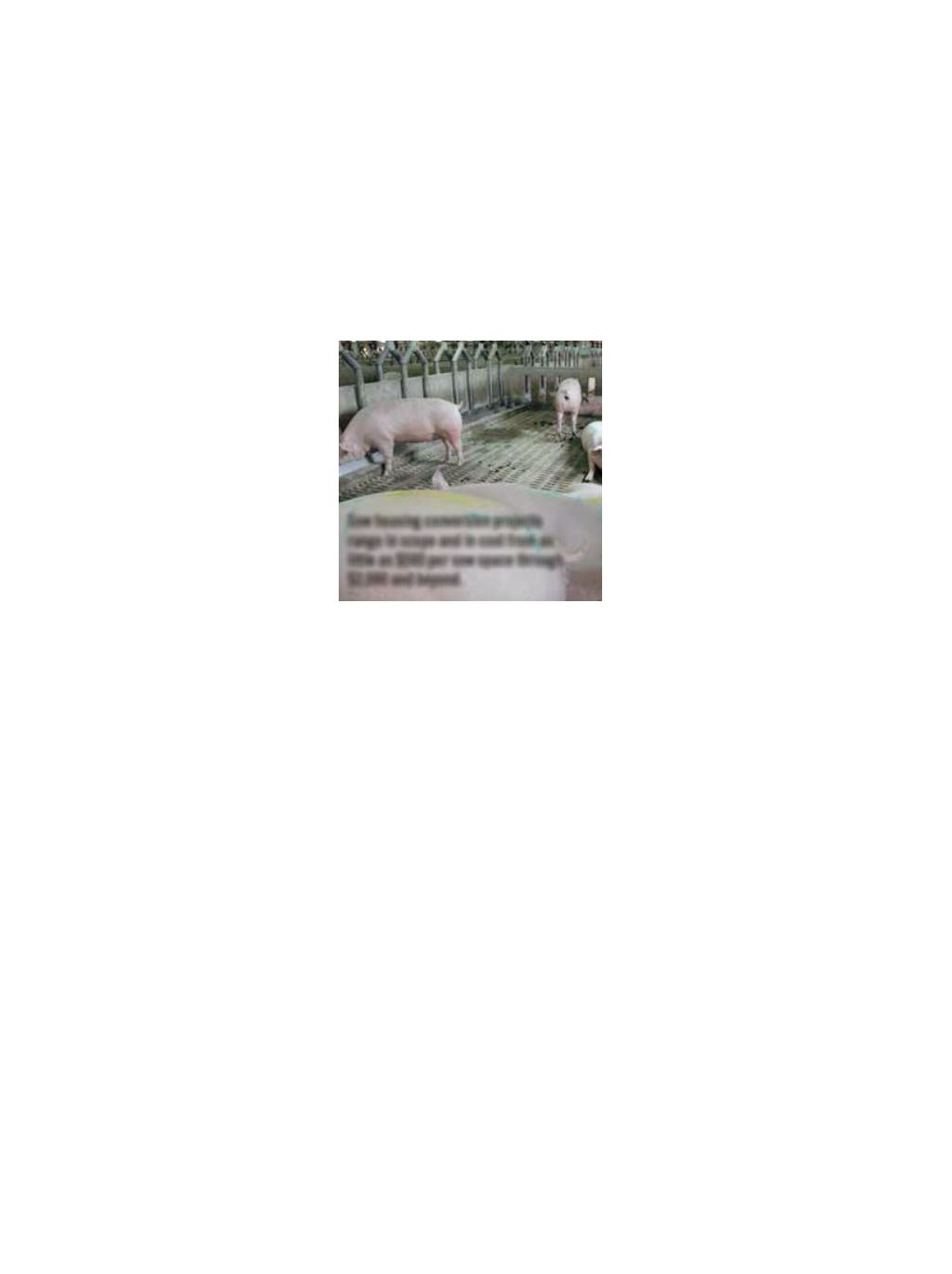
24
Better pork
August 2016
MAIN
FEATURE
N
ow may be as good a time
as any for group sow hous-
ing projects to comply with
pending measures in the new Canadian
Code of Practice for the Care and Han-
dling of Pigs. The measures take full
effect in 2024.
I
nterviews in early June with On-
tario equipment suppliers and builders
reflect active construction and planning
for sow housing projects to comply
with new measures in the code.
T
he rules require producers to in-
troduce more movement and/or group
housing within the next eight years for
gestating sows. Based on current data
showing 1.2 million sows and gilts in
Canada, a total shift to group housing
would cost millions of dollars, but the
cost to individual producers will vary
because conversions range in com-
plexity. Some conversions will involve
relatively minor interior renovations.
Others will involve the installation of
roomier, “freedom stalls” and high-
tech feeding systems designed to track
individuals and minimize conflict that
can arise among sows in groups.
B
etter to move now than, say, 2014
when the new code was introduced. It
was also the year one of the province’s
largest pork packers, Quality Meat
Packers Limited in Toronto, went
bankrupt leaving millions of dollars
in consequences for the firm’s hog-
farming creditors in Ontario. That
incident followed a period of distress-
ingly low hog prices and disruptive U.S.
country of origin labelling (COOL) for
imported pork.
B
ut the end of COOL, together with
improved hog prices and Canada’s
relatively weak dollar position relative
to U.S. currency, has strengthened the
position of Ontario growers.
S
tatistics Canada estimates show a
slight decline in hog farms nationally
to 6,965 during 2015 but an increase in
hog population. As of Jan. 1, StatsCan
counted 1.2 million sows and gilts, up
1.6 per cent from January, 2015.
C
anada exported 16.4 per cent more
hogs in 2015 compared to 2014. Do-
mestic hog slaughter rose 4.2 per cent
to 21.3 million head.
H
og industry economist Ken McE-
wan counts several current plusses in
all this.
“
Ontario is still very fortunate in
that we still have two packers,” he said,
referring to the province’s largest pack-
ers, Sofina Foods Inc. and Conestoga
Meat Packers, in a telephone interview
from his office at the University of
Guelph’s Ridgetown College. And there
are opportunities for smaller packers
to grow.
“
We still have a large urban mar-
ket that needs to be served,” McEwan
notes. “Close to a third of Canada’s
population lives in Ontario.”
P
roximity to U.S. markets and
current processing capacity in Quebec
capable of accepting Ontario hogs are
also positive factors, McEwen said.
A strong exchange rate advantage,
relatively stable feed costs and relatively
strong hog prices make what McEwen
describes as “a pretty nice mix” for
Ontario producers.
A
lthough individual decisions will
depend on the financial position and
planning of individual farm opera-
tors, McEwen figures it’s a good time
generally to be looking at capital
improvements. That’s particularly so in
operations with depreciated buildings
and equipment.
Projects will range in scope
P
rojects range in scope and in cost
from as little as $500 per sow space
through $2,000 and beyond. It can be
everything from reworking existing
buildings and retaining old school floor
feeding to complete new buildings and
turnkey installation of more costly
electronic feeding systems.
“
It’s kind of like renovating your
house,” FGC Ltd. designer Murray
Elliott said in an interview from the
construction company’s Sebringville-
area office. “The variation is large.”
S
imple adjustments can cost as little
as $7 to $10 a square foot. Add new
digital feeding equipment, structural
complications or personal improvisa-
tions, the costs double and triple.
A
lthough they’ve done some
renovations and new builds already for
group housing, FGC expects a gradual
increase in business as 2024 approaches,
Elliott said.
“
With a lot of people there’s no
huge hurry right now,” he said. “If their
equipment is still good, they might as
well wear it out, right?”
P
roducers approach such upbeat in-
dustry forecasts with caution. Veteran
Perth County grower Doug Ahrens of
Sebringville, an early adopter of group
The loose housing revolution: Pinpointing the right
time to build
Investment in sow-housing conversion will vary from producer to producer. Whether the project be
large or small, there is no better time to get started than the present, suggests one industry expert.
by JIM ALGIE
Sow housing conversion projects
range in scope and in cost from as
little as $500 per sow space through
$2,000 and beyond.